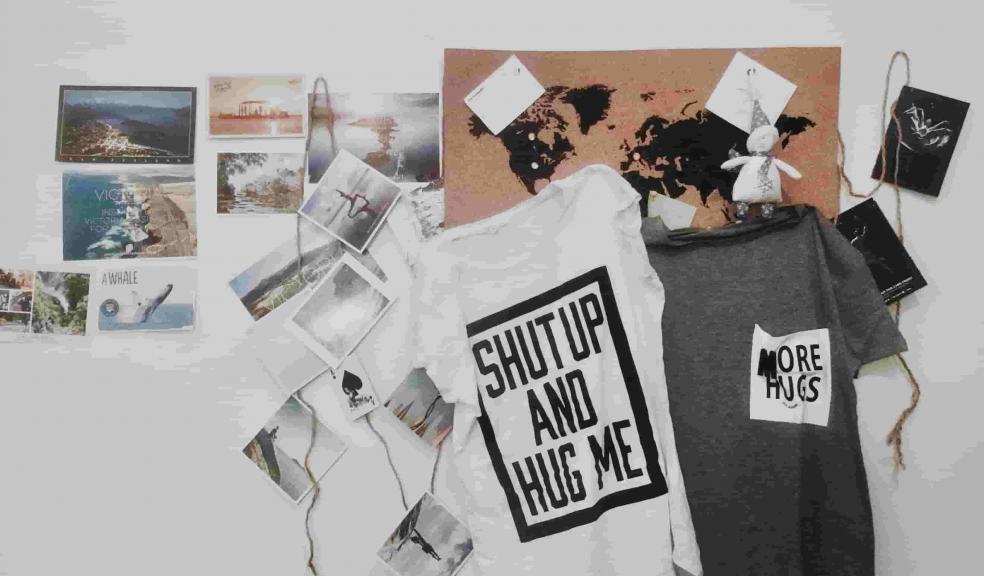
DIY screen printing t-shirts at home
Screen printing is much easier than you probably think. It also does not cost nearly as much to get started as most people believe. Sure, you can spend a fortune outfitting your entire basement or garage with fancy screen printing equipment that’s capable of customizing garments with lightning speed.
The frame
A frame is fundamental for screen printing. You can buy a cheap set of a frame from the market. However, it is more fun to make one at home. It is easy, and you can be more innovative with a homemade frame. For instance, you can keep sizes of your own choice for different types of t-shirts. For instance, 16"x16" frame size for adult t-shirts, 12"x12" for youth tees, and 7"x7" for the smallest size of the t-shirt. These sizes will give you sufficient room to work with the designs, along with some room to tape off the edges to avoid bleeding.
You can use scrap wood 2x2 pieces to make these frames for a sturdy frame with a heavy lip to contain the ink or dye during printing. Glue the measured pieces of wood together, and the frame is ready for the screen.
Attach the screens
The next step is attaching the screen to the frame. The Mesh fabric or a silkscreen work as best screens. Cut a piece of your chosen fabric for each frame. Leave sufficient overhang to wrap around the frames. Attach the fabric with a staple gun. Use help to ensure enough tension in the screen. You need to pull the fabric tight while stapling it, but be careful that the staples do not rip the fabric.
Apply photo emulsions
Once your frame and screen are ready, it is time to apply the photo emulsion. The emulsion reacts to light, so you must do the coating in a dark room. Moreover, you will have to keep the frame in a dark place until it is completely dry. If you want to keep it in a closet to dry, ensure that the light is not entering through cracks in the door. Photo emulsion is available in two parts. One container has the emulsion liquid, while the other has a solution to activate the emulsion process.You will need a squeegee to apply the emulsion.
Expose your screen with the chosen image
The next step is to choose the image you want to print and transfer it onto the screen. Take the design in your hand, face upward, just the way you want to see it on your t-shirt. Flip it over and put it flat on the screen. Place a clean glass piece over it to press the image tight against the screen.
Many tutorials guide you to use a lightbox, but we give you an easy alternative. All you need is a lightbulb of 150 watts. Now you need to expose the image to the light. The emulsion container has all the instructions, including the required time to expose the image to the light. It primarily depends on the screen size. The instructions will also guide you about the distance that you should maintain between the lights source and the screen. You will also need something matte black as your screen holder during the exposure. It can be a black chalkboard, black cardboard, or a bristol board. Set the timing and distance as per the instructions. Don’t disturb the screen during the exposure.
Wash away
After the exposure time, remove the piece of glass that was holding the image tight against the screen. Also, remove the paper or transparency cutout. You will instantly see a pale image. The emulsion around your image will be cured to become hard, leaving the image part. The image part will wash away under a high-pressure tap. You can use your garden hose or a showerhead to wash your screen. Use lukewarm water with a focus on the image. Keep spraying until the emulsion washes away and the design starts to appear. The result will be your first screen.
The final step
Once you have got your screen, the final result is just a few minutes away. Buy blank t-shirts that have the suitable fabric for screen printing. Many vendors sell DIY t-shirts for the sole purpose of custom screen printing. You can use the screen printing on tanks, tees, hoodies, or any style that you want. Spread your garment on a flat surface. Make sure to iron out any creases or wrinkles as they can distort the design. Place the silkscreen in a way the screen is directly pressed against the shirt. Apply the dye or the ink on the top of the image. Drag the ink down using a squeegee without applying pressure. This process is known as “flooding.” Repeat the process in the same direction with a bit of pressure. Make sure that you are applying sufficient pressure to force the dye through the screen. Carefully take off the screen. Hang the t-shirt to dry. If every step goes well then it is time to enjoy your custom screen printing results.